The history of human flight and the aerospace industry have early beginnings. By 1,000 B.C., Chinese scouts on kites monitored enemies, and by the 16th century, inventors were experimenting — often tragically — with devices that simulated birds’ wings. The 18th century saw the rise of hot air balloons. The next century brought steam-powered aircraft. After the Wright brothers made their first glider flight in 1900, airplane development kicked into high gear — and it hasn’t stopped.
The aerospace industry is continually exploring new methods to increase safety and reliability while decreasing costs. The 21st century brings high-tech possibilities to the field. Three types of technology — additive manufacturing, wearables, and cloud computing — are on the verge of making great changes in air and space travel. They’ll shake up the status quo — in a good way.
Aerospace industry is driving innovation
Build it up
Additive manufacturing — also known as 3D printing — produces lightweight components to exacting specifications. The process offers advantages for aerospace manufacturers:
- Cost: A single 3D printer can create multiple parts. The components don’t need a specialized production machine. This saves money on power and raw materials. In certain cases, individual parts can be combined into one unit to reduce assembly time and mistakes. Also, costs won’t soar if a single specialized piece is needed. The 3D printer doesn’t care if the input is for one item or 1,000. Producing upgrades and modifications are simple. Manufacturers don’t need large storage areas for replacement parts since they can be made as needed.
- Energy: Additive manufacturing materials are both strong and light — in some cases, up to 60 percent lighter. Lighter aircraft are more fuel-efficient, so they cause less pollution. Airbus has used certain 3D-printed engine parts since 2015. That same year, GE started producing 3D fuel nozzles for the LEAP engine, which also sports additive-manufactured fan blades. Boeing is a leader in 3D technology, using thousands of these parts in at least 10 aircraft production programs. Manufacturers are also investigating new materials to increase components’ efficiency and effectiveness.
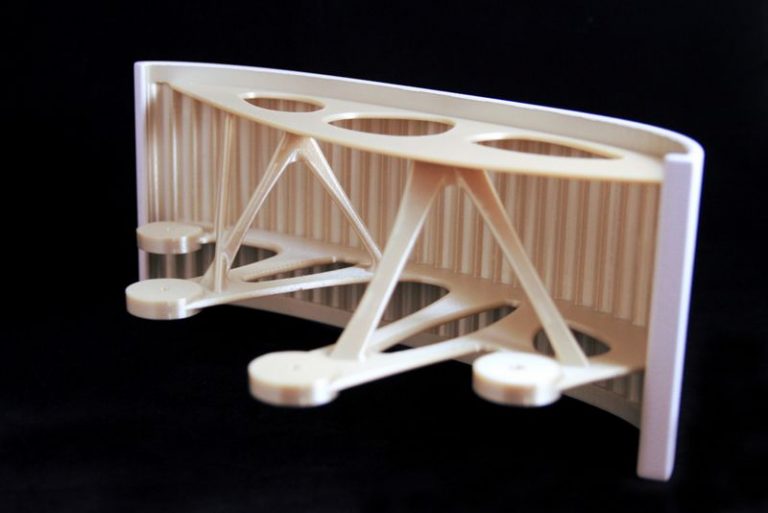
Put it on
Move aside, Google Glass. Wearable technology is one of the next big things in both the commercial and defense aerospace industries. During the manufacturing process, wearables give workers immediate and continual access to important information and increase opportunities for collaboration. The benefits include:
- Reduced error and, therefore, improved quality
- Boosts productivity
- Simplifies production
- Enhances worker safety
Airbus and Accenture, a technological consultant, joined forces to include wearables during production. A pilot program used smart glasses to mark cabin floors for seat placement. The devices let workers easily see all the required measurements. The job was completed in one-sixth the standard time — and with no mistakes. Additional manufacturing applications include:
- Accessing experts to answer questions quickly and accurately
- Monitoring workers’ health and safety
- Guiding workers step-by-step through complex processes
While wearables are used in manufacturing, they also have great potential during both quality control and aircraft service time. Smart glasses offer the promise of speeding up work while simultaneously limiting errors.
However, wearables bring security concerns. If massive amounts of manufacturers’ data are stored and transmitted, information systems must be safe from breaches. There must be preventative measures in place to keep competitors and other hackers out of a company’s records.
Push it up
Physical space for manufacturing, quality assurance, and storage is limited. The reality of cloud computing expands possibilities for the aerospace industry. Relying on the cloud to cache information enhances communication, cooperation, and speed while decreasing costs.
For instance:
- The creation of new tools and machines has traditionally been time-consuming and expensive. Using the cloud to document the journey of development makes prior plans readily available for review.
- The ability to easily share information among divisions across a company increases opportunities for innovation.
- Cloud-based automation of maintenance, repair, and overhaul is more efficient and less costly. While inventories are reduced, service is quicker and more precise.
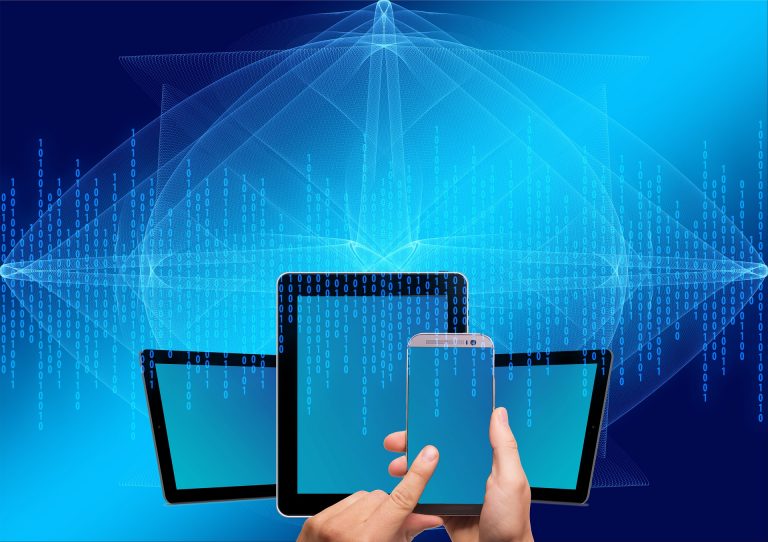
The U.S. Department of Defense has been an early explorer of cloud computing in its aerospace program. The ability to share information is vital, but the need for security is absolute. This necessary balance will lead to significant advancements in cyber protection.
Prove it
Innovations in the aerospace industry must undergo strenuous security and safety testing before they’re in the mainstream. For example, current aircraft assessments look at component functionality:
- Throughout acceleration
- At high altitudes
- During electromagnetic interference
- In response to vibrations
- Under extreme weather conditions
- After being struck by birds or lightning
Additive manufacturing, wearables, and cloud computing are no different. Testing includes:
- Incremental additions: Security is maintained for wearables by slowly adding functions. No new operations are considered until current ones prove to be well guarded.
- Multiple Layers: 3D printing is a multi-step process. Each stage — material development, machine selection, and operation set-up — is assessed, and the information gathered influences future decisions.
- Big Plans: Cloud computing capabilities, such as email consolidation and virtual applications, are tested at a single site. If all goes well, they can expand to other locations and agencies.
It’s been a long road. Centuries ago, people simply wished to fly. Now, humans regularly travel through the air, and space agencies are busy worldwide. Additive manufacturing, wearables, and cloud computing are poised to make significant changes in the aerospace industry. What’s next?